021 Industry Research Team
Jiayi Chen
Senior Analyst
Introduction
Semiconductors are an indispensable and vital component of electronic chips, providing circuitry support for various electronic devices like smartphones, automobiles, laptops, televisions, washing machines, and gaming consoles. However, over the past year, a shortage of chips has led to extensive disruptions in the consumer electronics manufacturing industry, with a particularly severe impact on the automotive production sector. Due to the chip supply constraints, many automakers have announced production cutbacks. The semiconductor materials industry is also an upstream part of the entire integrated circuit supply chain, serving as the cornerstone of the entire industry.
The quality of semiconductor materials directly influences the performance of integrated circuit products, making the stable supply of key semiconductor materials closely tied to the production activities of semiconductor manufacturers. It will also have a decisive impact on the development of the semiconductor market and the entire industry.

Industry Status
According to data released by the SEMI (Semiconductor Equipment and Materials International), the global semiconductor materials market showed a fluctuating trend in size from 2015 to 2019 due to the influence of the overall semiconductor industry environment. In 2019, the global semiconductor materials market was approximately $52.14 billion, marking a 1.12% year-on-year decrease. However, in 2020, driven by strong global demand for semiconductor products, the market size reached $55.3 billion, surpassing the 2018 level. By 2021, the market continued to grow steadily, with an increase of approximately 6%, reaching a market size of $58.7 billion. Furthermore, SEMI data indicates that semiconductor materials account for about 12%-17% of the entire semiconductor industry. Therefore, with the growing global demand for semiconductors, the semiconductor materials market is expected to continue its stable growth.
Currently, in the domestic semiconductor industry chain, the semiconductor materials industry is a relatively lagging sector, particularly in the part of wafer manufacturing materials, where dependence on imports can even exceed 90%. Looking at the production process, manufacturing bases are gradually moving closer to demand markets, which can reduce transportation costs. Manufacturers can respond to user demands promptly, accelerate technological research and development, and product iteration. This provides a substantial market space for the localization of relevant products. Therefore, strengthening technological research and development and industrial layout in the field of semiconductor materials, enhancing localization, is a significant direction for the current development of the domestic semiconductor industry.
The competitiveness and localization progress of the Chinese semiconductor materials industry can be divided into three levels based on the situation of specific products. The first level comprises products with technical standards that have already reached a globally leading level, with local production lines capable of large-scale supply, such as CMP polishing liquids, wet electronic chemicals, sputtering target materials, packaging substrates, and lead frames. The second level includes individual products with technical standards at a globally leading level, and local production lines can provide small-scale supply, such as electronic specialty gases and mask blanks. The third level, while achieving some technological breakthroughs, still has a considerable gap compared to international top-tier levels, such as photoresists and wet electronic chemicals larger than 8 inches.
The formation of these three levels is primarily due to varying entry barriers in different material industries, differences in the time Chinese companies entered the industry, and variations in accumulated technological expertise.

Materials
Photoresist
Photoresist is a crucial medium for transferring patterns in semiconductor manufacturing. It utilizes differences in solubility after a photosensitive reaction to transfer mask patterns onto a substrate. In the electronics manufacturing field, photoresist plays a pivotal role in producing fine circuitry lines. The photoresist process accounts for approximately 35% of the total chip manufacturing cost and takes up 40-60% of the entire chip production time, making it one of the core processes in semiconductor manufacturing. Currently, high-end EUV (Extreme Ultraviolet) photoresist is primarily controlled by companies in Japan and the United States. In mainland China, only KrF (Krypton Fluoride) photoresist is in mass production, while ArF (Argon Fluoride) photoresist products are still in the downstream customer verification stage, lacking actual mass production capability. Additionally, there is almost no technological reserve for the highest-grade EUV photoresist.
Mask Blanks
Mask blanks are a critical component in the semiconductor chip manufacturing process, used to transfer design patterns onto silicon wafers during the photolithography process. They are also commonly known as reticles, photomasks, or lithography masks. Throughout the chip manufacturing process, multiple photolithography steps are performed, with each step requiring a mask blank. The quality of each mask blank affects the accuracy and quality of photolithography. Leading wafer manufacturers globally, such as Intel, Globalfoundries, IBM, TSMC, UMC, Samsung, among others, have their mask blank production facilities to meet the needs of their chip manufacturing processes. However, in recent years, the trend of outsourcing mask blank production has become more evident, particularly for lower-end products with process nodes of 60 nanometers and above.
Sputtering Target Materials
Inside semiconductor chips, unit devices are composed of various layers, including the substrate, insulating layer, dielectric layer, conductor layer, and protective layer. Among these, dielectric and conductor layers require sputtering coating processes. In the field of integrated circuits, sputtering target materials mainly include aluminum, titanium, copper, tantalum, tungsten-titanium, and others. These target materials demand extremely high purity, typically requiring a purity level of 5N (99.999%) or above. Currently, major semiconductor chip target materials are dominated by Japanese and American giants, holding approximately 90% of the global market share. In Germany, Heraeus has almost monopolized the supply of tantalum powder raw materials and tantalum target blanks for semiconductor chips. On the domestic front, companies like Jiangfeng Electronics and Yoyi New Material have been rapidly rising in the field of target materials manufacturing, securing their place in the global market. However, semiconductor chip manufacturers have strict certification processes for their qualified target material suppliers, and each company has different certification requirements. Most suppliers find it challenging to bear the substantial financial and time costs associated with the certification process. Consequently, semiconductor manufacturers are not very inclined to introduce new suppliers, leaving limited opportunities for new industry entrants. This results in a highly concentrated industry.
Polishing Materials
Polishing materials mainly include polishing pads, polishing slurries, conditioners, and cleaners. Of these, polishing pads and slurries constitute the majority of the polishing materials market, accounting for over 80%. Polishing pads are typically made by blending polyurethane or polyester with saturated polyurethane, while polishing slurries consist of ultra-fine solid abrasive particles (e.g., nanoscale silica, alumina particles, etc.), surfactants, stabilizers, and oxidizers. The majority of the global polishing pad market, over 90%, is dominated by Dow Chemical Company. In contrast, Fujimi from Japan, Cabot from the United States, ACE from Korea, and others hold a significant portion of the global polishing slurries market. In China, Anchortech is filling the gap in domestic production of polishing slurries, while Dinglong Holdings is actively entering the polishing pad market, striving to catch up with the global leaders. With continuous advancements in chip manufacturing and packaging technologies, the demand for polishing materials is expected to increase further.
Electronic Specialty Gases
Various specialty gases, referred to as electronic specialty gases, are required during the production of semiconductor chips. These gases can be classified based on their chemical composition as general gases or specialty gases, or based on their application as dopant gases, epitaxial gases, ion implantation gases, light-emitting diode (LED) gases, etching gases, chemical vapor deposition gases, and balance gases, among others. In the Chinese market, first-tier companies like Hwatel Gas, Golden Hong Gas, Nanda Optoelectronics, and Jacques Technology collectively hold a 7.1% market share. These companies have achieved large-scale production capabilities and have a localized advantage in certain niche areas.
Wet Electronic Chemicals
Wet electronic chemicals, also known as ultra-pure high-purity reagents, refer to various high-purity chemical reagents used in semiconductor manufacturing. The global market is predominantly led by European and American companies, including Germany's BASF and Henkel, the United States' Ashland, APM, Honeywell, ATMI, Airproducts, as well as Japan's Sumitomo Chemical, Ube Industries, Showa Denko, Changelight, and Mitsubishi Chemical, among others. Currently, the localization rate of wet electronic chemicals in the semiconductor field in China remains relatively low. Especially for the processing of wafers larger than 12 inches, the localization rate is less than 10%. However, for 1μm processes, large-scale production has already been achieved, and chemical products for 0.18μm processes have also undergone research, with expectations for increased self-sufficiency. In terms of product quality, some leading companies have met international G5 standards, effectively promoting the localization of wet electronic chemicals.
Packaging Substrates
Packaging substrates represent the highest cost component within packaging materials. They serve as carriers for chips, providing protection and connection between upper-layer chips and lower-level printed circuit boards. These substrates enhance the thermal dissipation performance of chips, provide support, connect chips to printed circuit boards, distribute power, transmit signals, and enable communication between the chip's internal and external circuits. Currently, the main categories of domestically manufactured packaging substrates include Wire Bonding Ball Grid Array (WBBGA) substrates, Flip-Chip Chip Size Package (FCCSP) substrates, coreless substrates, and embedded passive components. Relative to high-end FCBGA substrates and substrates with embedded active components, the advanced substrate market in China remains relatively weak.
Lead Frames
Lead frames, as carriers for semiconductor chips, play a crucial role in welding and connecting the internal circuits of chips to external circuits (PCBs). They are an essential foundational material in the electronics information industry, serving as bridges connecting chips and external wires. Lead frames generally include TO, DIP, SIP, SOP, SSOP, QFP, QFN, SOD, SOT, and other types, and these types are mainly produced through mold stamping and etching methods. Due to the continuous increase in upstream raw material copper prices and the uncertainty of delivery times for Japanese lead frame equipment suppliers, expanding production in China is not straightforward, and the overall lead frame market is characterized by high demand and short supply. This situation may continue until 2023. Currently, among domestic products, Kangqiang Electronics holds a significant market share.
Bonding Wire
Bonding wires in semiconductors play a crucial role in welding chips to their mounts, serving as key electrical connections. In the past, bonding wires were typically made from a single material, but they have now evolved to include a variety of materials, including gold, silver, copper, aluminum, and related composite materials.

China's Semiconductor Materials Industry
Policies
The semiconductor industry, as a cornerstone of the information industry, is crucial for this sector's development. Currently, China's semiconductor industry heavily relies on imports, posing significant supply chain security concerns, which is detrimental to the industry's growth. As a result, the Chinese government has shown a strong commitment to the development of the semiconductor industry in recent years. Various national-level departments such as the Ministry of Industry and Information Technology, the National Development and Reform Commission, and the State Council have introduced a series of encouraging policies aimed at supporting and guiding the development of the semiconductor materials industry. Key materials like photoresist and sputtering targets have been included in the list of priority new materials for development.
Additionally, at the local level, several regional governments have released policies to boost the growth of their local semiconductor materials industries.
Capital
Between May 2021 and May 2022, China's advanced semiconductor materials sector witnessed a total of 91 transaction events, indicating a continuous influx of capital. Simultaneously, China's secondary market for the semiconductor industry saw signs of recovery in the first half of 2022. Furthermore, the first phase of the National Large Fund is in its collection phase (2019-2024), while the second phase began implementation in October 2019, with the potential to mobilize over 1 trillion RMB in total social capital. The focus of this fund is clear: it tilts toward the semiconductor materials industry, introducing financing policies to encourage semiconductor materials companies to expand their operations through the capital market. The government is actively guiding and promoting more investment in R&D and production of semiconductor materials. According to the plan, the second phase of the National Large Fund will mainly concentrate on the upstream areas of the semiconductor industry, such as semiconductor equipment and materials, with the goal of improving the vital industry chain in the semiconductor sector.
Technology
For many years, core technologies in the semiconductor industry have been primarily developed by countries with an early start, such as the United States, Japan, and South Korea. In comparison, Chinese companies have had relatively limited investments and accumulations in this field. However, in recent years, the Chinese integrated circuit industry has been rapidly growing, and R&D efforts in the semiconductor materials sector have been progressing swiftly. Breakthroughs have been achieved in certain areas like photoresists. As technology continues to upgrade and iterate, the localization of semiconductor materials is expected to accelerate. As of December 2021, the primary source of global semiconductor materials' major patents was China, with Chinese semiconductor materials patent applications accounting for 32.05% of the global total, followed by the United States at 23.78%.
Industry
The global semiconductor industry supply chain has undergone three shifts, with the latest shift towards mainland China starting in 2010. With the construction of new wafer fabs and capacity expansion, mainland China has accelerated its acceptance of semiconductor capacity and entered a period of rapid growth. This, in turn, has led to a significant increase in demand for complementary semiconductor materials, continuously expanding the market. According to data from SEMI, from 2017 to 2020, a total of 62 new semiconductor wafer fabs were constructed globally, with 26 of them located in mainland China, accounting for 42% of the global total. Furthermore, global semiconductor materials production has shown a noticeable shift towards locations such as Taiwan, South Korea, and mainland China. This shift helps China take on more semiconductor capacity. By 2021, the scale of China's semiconductor materials industry had surpassed that of South Korea, making it the second-largest globally, second only to Taiwan. Over the next few years, the Chinese semiconductor materials industry is expected to steadily grow at an annual rate of approximately 20%, with the market size projected to reach $25 billion by 2025, gradually closing the gap with the Taiwanese market.
Enterprises
Semiconductor manufacturing is a complex process, requiring substantial financial investments and the use of advanced equipment and processes. This makes the industry have high technical and financial entry barriers. The manufacturing process involves over 500 steps, including cutting, masking, etching, laser marking, chemical mechanical polishing, photolithography, developing, sputtering, deposition, purification, and more, contributing to high technological barriers in the semiconductor materials industry. Significant capital is required in the early stages of research and development, customer validation, and production processes. The customer validation process, in particular, often takes several years, necessitating substantial financial support as it is a critical part of a company's survival. Given the highly technology-intensive nature of the industry, talent recruitment and development present a significant challenge. The field covers various scientific and engineering disciplines, including plasma physics, micro-molecular dynamics, structural chemistry, spectroscopy, vacuum mechanical transport, and more. The rapid pace of technological iterations also requires industry professionals to possess high learning and comprehensive skills. The customer validation phase is crucial before semiconductor products enter the market. This process is lengthy and complex, demanding a great deal of patience and financial support for research and development before securing production orders. Additionally, customers must have the willingness and capacity to conduct validation of new products. The entire validation process is a mutual selection. Consequently, startup companies may encounter obstacles in the validation phase until they gain sufficient market trust.
Tongcheng New Materials
Tongcheng New Materials, with its dual pillars, Kehua and Beixu, is a dominant force in China's photoresist sector. It has achieved large-scale production of KrF photoresist. Kehua is the sole Chinese photoresist company listed in the top eight globally by SEMI. Meanwhile, Beixu Electronics leads the domestic panel photoresist market and holds over 45% of the TFT positive photoresist market share in BOE.
Jingrui Electronic Materials
Jingrui Corporation has successfully developed some ultra-pure high-purity reagents that meet the highest international purity standards (G5). This breakthrough breaks the foreign technology monopoly. The company has also established various industry standards.
Nanda Optoelectronics
Nanda Optoelectronics has overcome several significant technical challenges, including industrializing the full range of MO source products under the National 863 Program, researching and industrializing high-purity electronic gases (arsine and phosphine) for the National "02 Project," and industrializing ALD/CVD precursors. These achievements have filled multiple technical gaps in China.
Hwatsing Gas
Hwatsing Gas's photoresist gas blend has received ASML certification, making it one of only four companies globally to earn this recognition. It is also the sole Chinese company to achieve ASML certification.
DuoFuDuo
Following on-site audits and multiple rounds of online testing, the company has successfully entered TSMC's qualified supplier system. It is about to commence large-scale supply of high-purity electronic chemicals to TSMC. This marks the point at which the company's domestically produced electronic-grade hydrofluoric acid has reached international standards.
Anji Technology
Anji Technology has successfully filled the gaps in the domestic integrated circuit field for chemical mechanical polishing slurry and certain functional wet electronic chemicals. The company has contributed to China's ability to independently supply these materials in this sector.
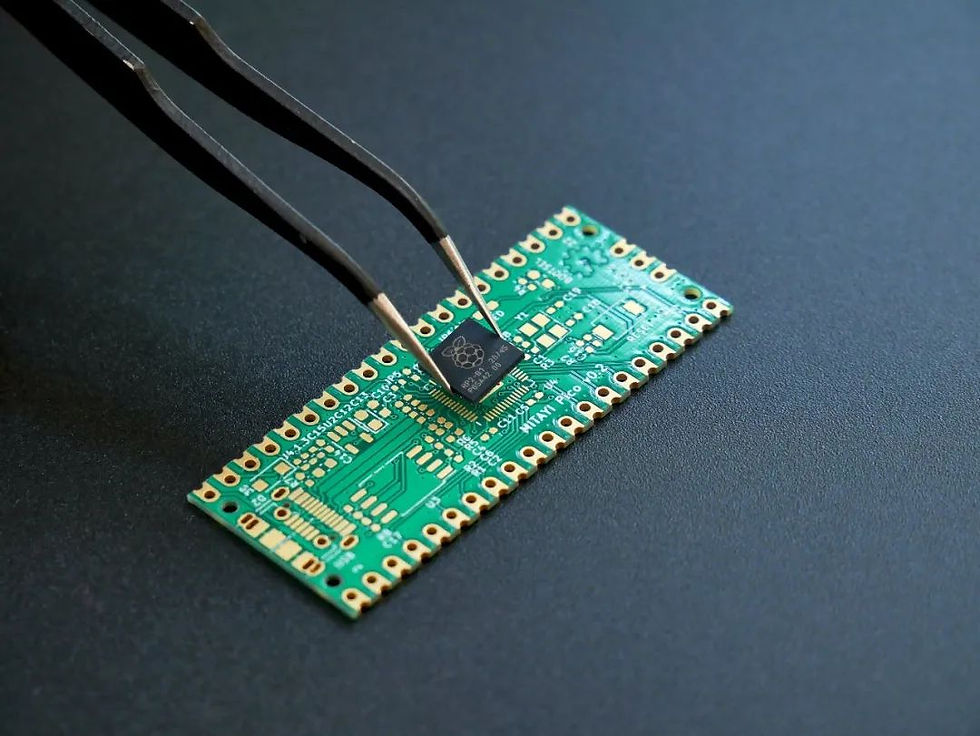